[Surface treatment]Anodizing, chemical nickel process
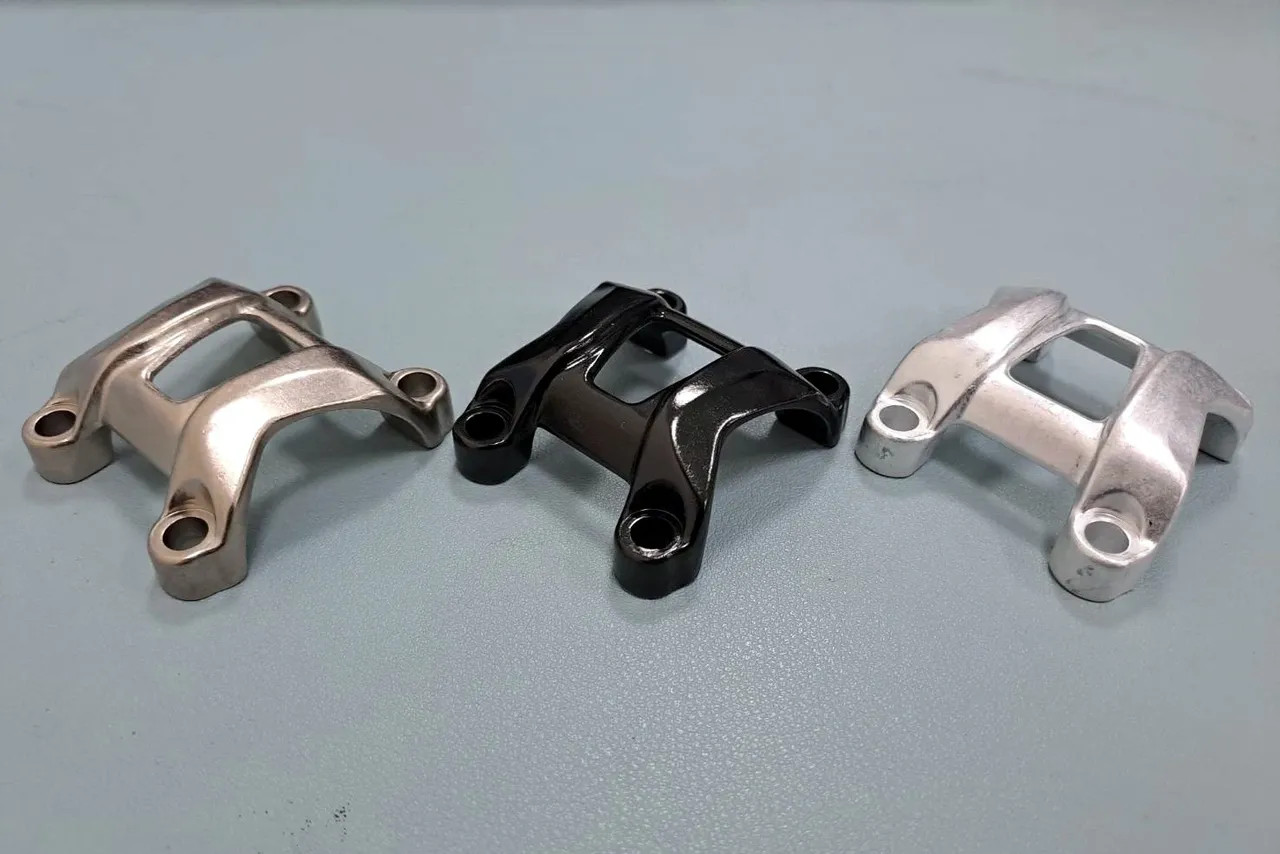
The same workpiece can present different effects and functions through different processes according to different needs. As shown in the picture above from right to left: aluminum alloy material, anodized treatment (black) and chemical nickel. Next, we will briefly introduce each process to let you understand.
Process : Anodizing
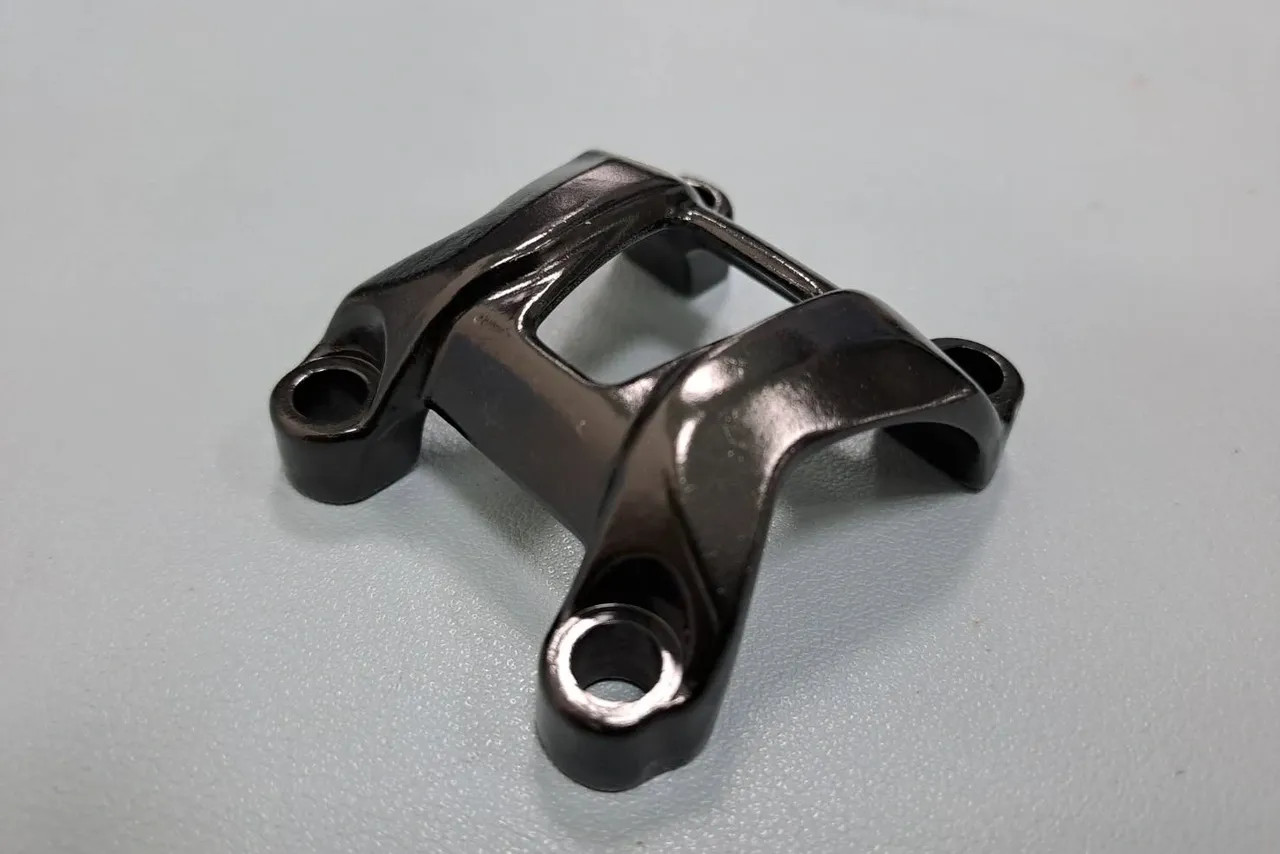
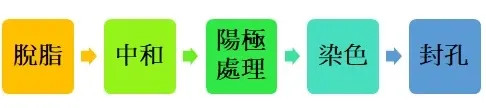
Neutralization - Since there is an oxide layer on the surface that cannot be removed by degreasing, a neutralizing agent is used to dissolve the oxide film to obtain the cleanest metal surface.
Anode - The workpiece is used as an anode through electrochemical methods, and electrolytic oxidation is performed to form an oxygen layer with tight hexagonal holes.
Dyeing - The anodized workpiece is immersed in organic dyes and the desired color is obtained through the length of immersion time.
Sealing - Use a sealing agent to seal the dye filled in the anode holes under high temperature conditions to prevent it from flowing out, so that the workpiece can maintain a beautiful appearance.
This is the simplest process, and there are various effects corresponding to different processes. If you are interested, you can try it!
Process: Chemical nickel
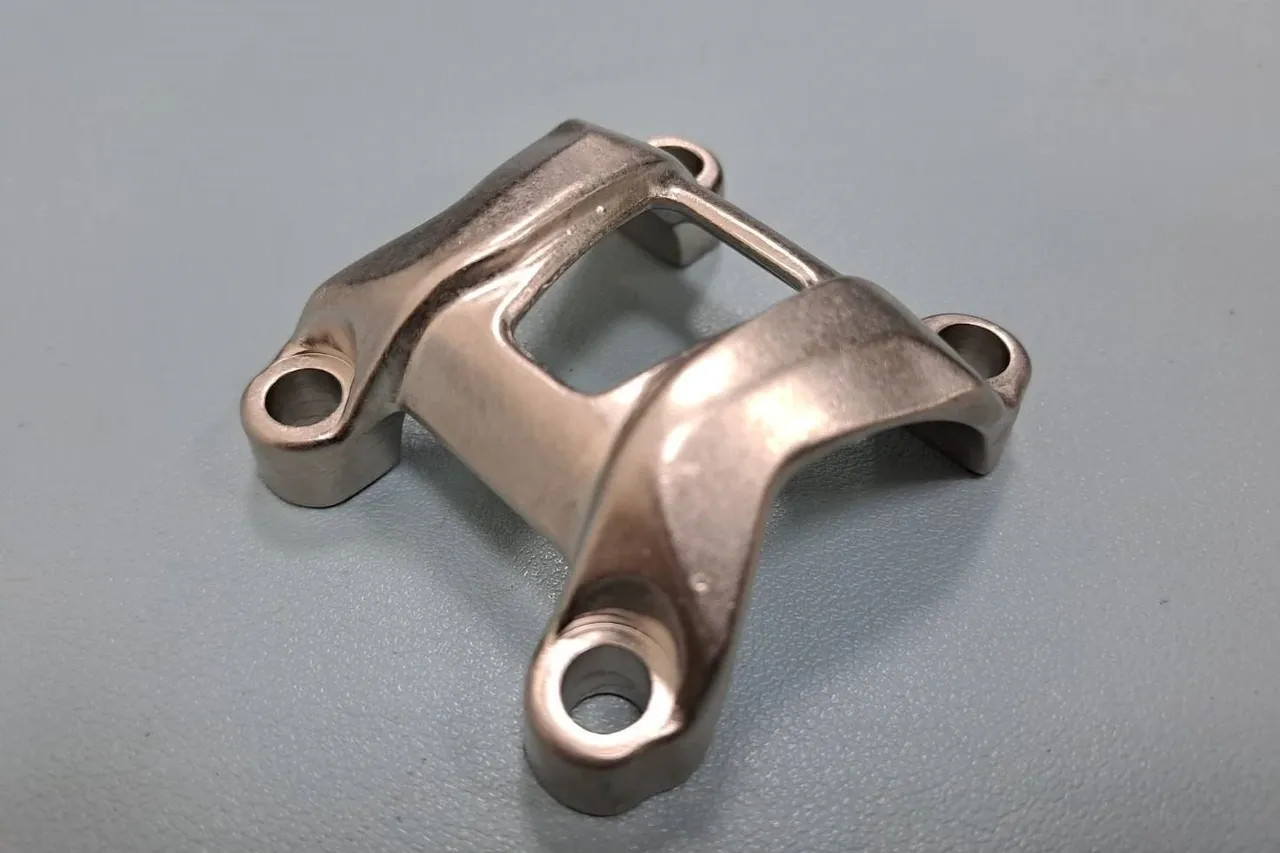

Degreasing - surface dirt is removed through immersion cleaning so that the workpiece can remain clean for subsequent processing.
Micro-etching - micro-roughening of the surface, with good coverage during the first zinc replacement.
Film removal - In addition to removing the oxide film, it also cleans the powdery matter produced by micro-etching.
Zinc replacement 1 - Dissolve the oxide film and perform a replacement reaction. The zinc layer obtained in the first pass is rough, porous and has poor adhesion.
Zinc stripping - gives the aluminum surface a uniform and detailed activated state.
Zinc replacement 2 - The second zinc replacement can obtain a thin, uniform and fine zinc layer with strong bonding force.
Electroless nickel - using electroless nickel (or electrolytic nickel) to coat the surface with nickel metal, which not only prevents nickel from oxidizing, but also improves wear resistance and corrosion resistance.
After zinc replacement, in addition to nickel plating, copper, chromium, silver and other metals can also be plated and applied to the required products.