[Aluminum] "Sealing treatment" in anode
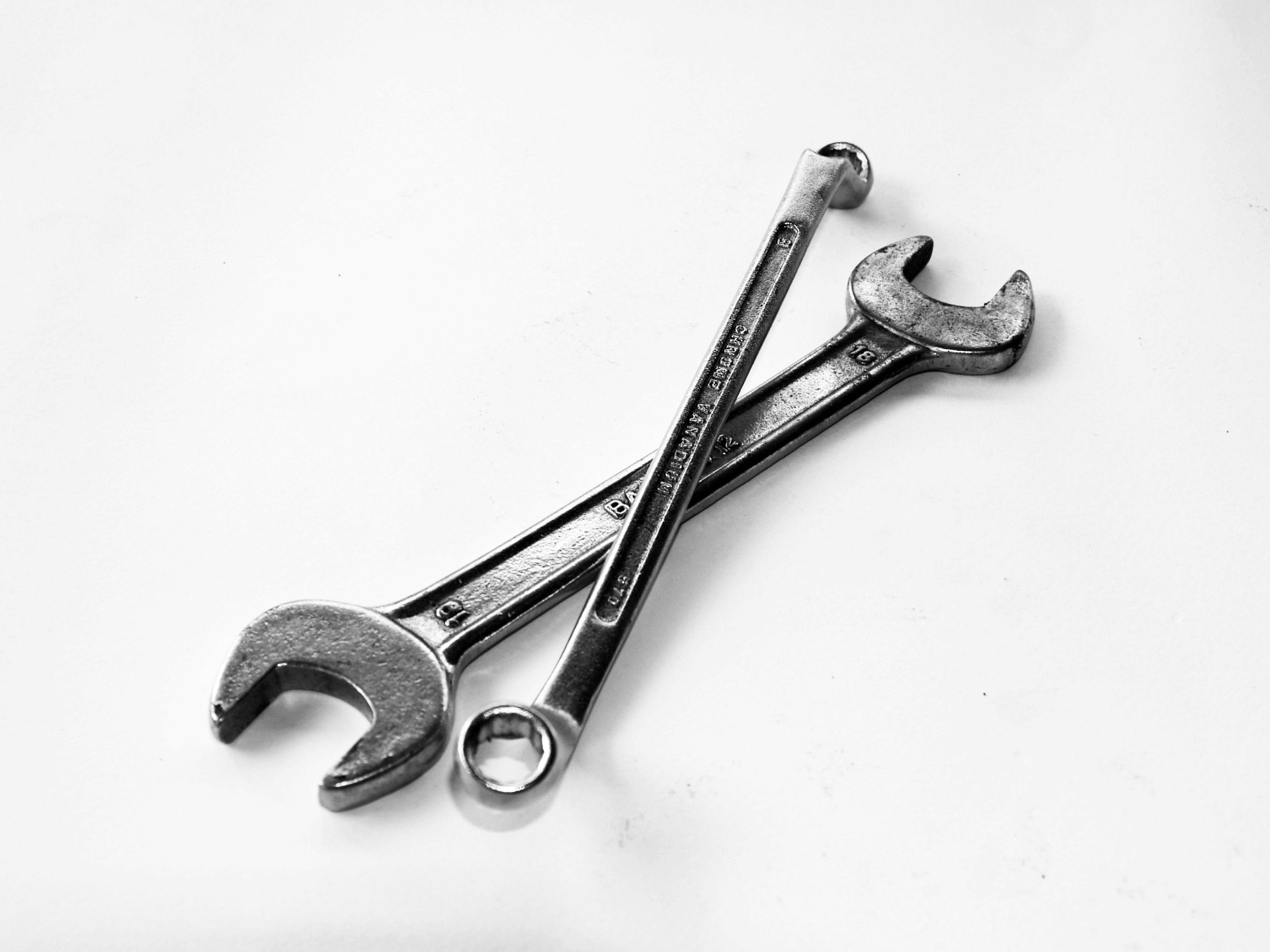
Sealing treatment is the last and most important treatment in the anode treatment process. When the sealing effect is good, it can improve the corrosion resistance of the product. If the product is dyed, it has a blocking effect so that the dye will not flow out of the surface. The principle of sealing treatment is mainly to seal the pores in the oxide film through physical and chemical means, thereby preventing moisture and other corrosive substances from entering the interior.
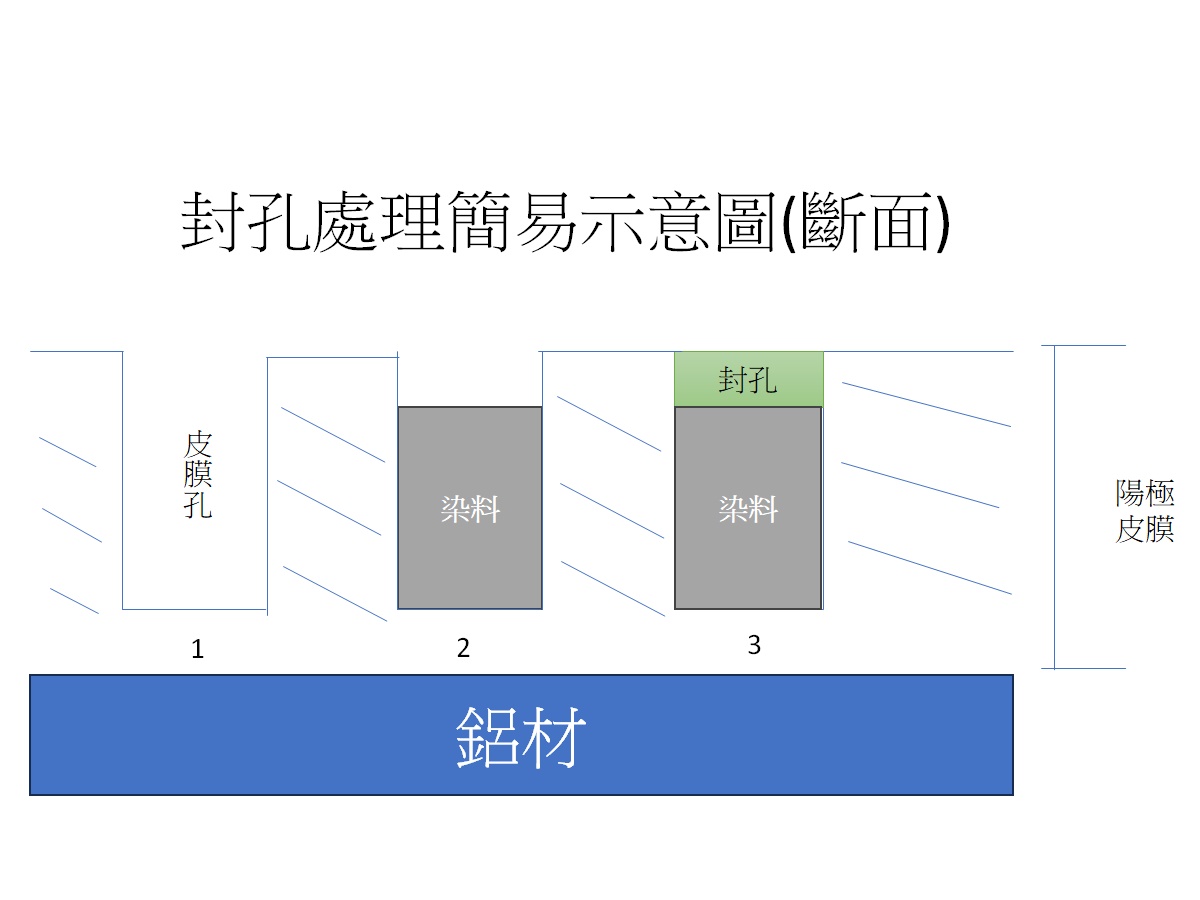
Principle of sealing treatment (with staining)
Regarding the hole sealing process, we use a simple schematic diagram (above) to illustrate:
- After anodizing, an oxide film is formed, with a common thickness ranging from about 5 to 25 um (depending on demand), and a film pore size of about 20 to 50 nanometers.
- In order for the finished product to show its color, it is directly immersed in the dyeing tank to fill the pores of the film with dye, and then the dyeing time is adjusted according to the depth of the color.
- Finally, it enters the sealing tank and uses hydration to fill the holes in the film to prevent dye from flowing out and improve the corrosion resistance of the finished product.
Sealing method
Hot water sealing (nickel acetate): This type is the most common anodized sealing. Nickel metal ions enter the pores of the oxide film to fill them. This prevents foreign matter from penetrating into the pores and corroding the workpiece, and it can also be effectively blocked. The dye is prevented from flowing out, allowing the product to maintain its proper color. Disadvantages: It needs to be used at high temperatures. Water evaporates easily and needs to be replenished at any time, and personnel must always pay attention to temperature changes to avoid danger.
Room temperature sealing (nickel fluoride): Mostly used for non-stained objects or building materials, because it can be carried out at room temperature and is relatively easy to manage. The disadvantage is that the ingredients contain fluorine, which requires additional treatment in the wastewater treatment part. The treated workpiece may have a light green oxide film, so testing and evaluation are required before use.
Hot water sealing (additive): A method used in the early days when corrosion resistance was not discussed. High-temperature water combines with aluminum oxide to form hydrated alumina, which plugs the holes through the hydration reaction; some manufacturers use this method in order to improve the sealing Effectiveness, additives will be developed and added for use. Disadvantages: This method has poor corrosion resistance and dye locking, and is no longer suitable for current related products.
Nickel-free sealing (non-nickel series): Due to the rising environmental awareness, nickel emissions have become increasingly strict. Therefore, in recent years, various manufacturers have tried their best to develop alternatives; however, the drugs developed must be tested after use. , all failed to achieve the same performance as nickel acetate, resulting in a delay in the development of nickel-free sealing.
Sealing treatment is one of the most important processes in anode treatment. If the chemical solution is well managed, the product will have good resistance and will not fade easily. If the chemical solution is not well managed, in addition to poor corrosion resistance, the alumina powder will adhere to the surface. The surface of the workpiece needs dedicated personnel to analyze and manage it at all times to maintain the best performance of the chemical solution.